THE USE OF ROLLER COMPACTED
CONCRETE
Francisco Rodrigues Andriolo
pág. 13
3.1.2-
General Development
Of the total number of
dams built worldwide [3.24] until 1950, excluding China, 38% of the
dams equal or greater in height than 15m had been built in concrete.
Between 1951 and 1977, this number dropped to 25%. Between 1978 and
1982, this number decreased even more, dropping to 16.5%.
The
decline in the construction of concrete dams took place in a time when
the number of arch dams in narrow valleys was increasing. The reduction
happened, however in dam sites situated in wide valleys, where concrete
gravity dams were substituted by embankment or fill type dams, with
a lower construction cost. This cost reduction originates basically
from a greater efficiency in the equipment used.
Nevertheless,
in contrast to a greater economy, the fill types dams presented - and
still present - a greater probability of failure as mentioned in [3-24].
In the United States, there has not been a failure of a concrete dam
higher than 15 m since 1928. Outside the United States, the most recent
failure of a concrete dam was that of Malpasset Dam, in France in 1959.
This was a 61-m high arch dam, in which sliding of one of the abutments
occurred over the length of a fracture plane. On the other hand, during
the last 60 years, hundreds of failures have happened with fill type
dams. The main causes are the overflowing during a flood (as was the
case in Tous Dam) and the internal erosion of the fill material (as
at Teton Dam).
As
a result, it became necessary to find a new type of dam that combined
the superior safety of concrete dams with the efficiency of the construction
method of fill type dams. From this basic idea, and by way of several
different methods, RCC dams were developed.
The
RCC construction method evolved not only from the efforts of some influential
concrete dam designers but also from the work of geotechnical engineers
who traditionally design earth and rockfill embankments. Their combined
efforts have produced a concrete dam built with methods usually associated
to earth dam construction. The product is a low-cost dam with the same
inherent safety as a conventionally placed concrete dam.
An
authentic forerunner of this dam type is the Alpe Gera Dam, completed
in 1964 in Italy [3-02]. Here, an attempt was made to reduce the cost
of construction while maintaining the cross section of concrete gravity
type dams. Part of the economy was obtained by reducing the cement content
in the concrete used in the interior of the dam body, where stresses
are lower and demands for durability, minimal. Most cost reduction however,
came from the use of embankment construction methods. Concrete was extended
in horizontal layers [3-25; 3-26], a method currently called [3.27]
"E.L.C.M.- Extended Layer Construction Method" by the Japanese.
It was used at Nunome Dam - 72m high, volume of 330,000 m3 in 1989.
The difference between construction methods used at the Alpe Gera Dam
and known as "E.L.C.M.", and those used in a roller compacted
concrete dam, is that the lean concrete was consolidated by internal
needle vibrators mounted on tractors, instead of using external compacting
with rollers.
In
the 1970's, the evolution of the concept of RCC dams followed different
roads:
-
Dams
built with lean mixtures, with a content of cement paste of 70 to
100kg/m3, and with the placing of mortar between layers. This alternative
was developed by the United States Army Corps of Engineers and other
researchers and their first important work was the Willow Creek
Dam (United States), completed in 1982;
-
Dams
with high-paste contents of binding material from 150 to 270kg/m3,
with a high proportion of fly-ash. Examples of these are the Upper
Stillwater Dam (United States, 1987) with more than 1,125,000m3
of concrete with a mix of 247kg/m3 of binding material.
-
Dams
of average content of paste, with mixes between those of the two
previous groups. Les Olivettes Dam (France, 1987), with 130kg/m3
of a special cement, and Craigbourne Dam (Australia, 1986), with
170kg/m3 of binding material, are examples of this type.
-
Japanese
dams known as RCD: Roller Compact Dams. The difference with the
previous types is not the content of binding material (until now,
it has oscillated between 120 and 130kg/m3), but basically, the
method of placing on the job. Layers 50 to 100cm thick are extended
in several sublayers and are all compacted in one operation, instead
of compacting each sublayer. Before compaction, cuts are made in
the fresh concrete every 15m using a vibrating cutting tool and
crack or fissure inducers are inserted. Bonding or union between
layers is assured by way of careful cleaning of the surface and
the extension of a thick layer (15mm) of mortar. The first application
of this technique occurred at the Shimajigawa Dam (1980); to date,
more than twenty works have been carried out. The most remarkable
examples are the Tamagawa Dam (1986), with a total volume of 1,154,000
m3, and the Miyagase Dam (1994), with 1,930,000m3 of compacted and
conventional concrete.
-
Brazilian
Dams, with a cement content of 70 to 100 kg/m3, with high fine content
(8% to 12% finer than 0,075mm) and the placing of mortar between
layers and a conventional mass-concrete upstream membrane face.
The fine material used can be silt (as used in Saco Nova Olinda
Dam) without pozzolanic activity or can be crushed powder filler,
from a certain rock, as used in Jordão and Salto Caxias Dams,
with low pozolanic activity.
Other
than the Italian precedent, the Alpe Gera Dam, and other cases of embankment
type dams such as the repair of Tarbela Dam (Pakistan, 1974), the first
dam was the Shimajigawa Dam (Japan, 1980) mentioned above.
RCC technology evolved considerably afterwards and numerous examples
of RCC dams emerged in countries such as United States, Japan, South
Africa, Australia and Spain. The ample approval of RCC dams can be explained
by the great advantages of this technology, among which can be emphasized:
Figure
3.04- Saco Nova Olinda Dam - the first Brazilian RCC dam and the first
arched RCC dam in the world.
-
as
compared with conventional concrete dams:
- superior rate of construction (can reach 2-2,5m per week);
- large-scale use of conventional equipment (dumpers, bulldozers,
rollers);
- as a consequence of the previous point, reduced costs;
- less impact on the environment.
-
as compared with embankment or fill type dams:
- shortening of the time for completion, by placing with similar
rates reduced volumes (ratio from 1:4 to 1: 5);
- may perform as a spillway over the dam;
- shorter outlet conduits and intakes. Intake tower abutting against
the dam and not freestanding;
- shorter river diversions during the construction;
- as a consequence of the aforementioned, a considerable construction
cost reduction;
- less impact on the environment due to less quantity of materials
required, which also results in a reduction in traffic problems,
dust and scars in the zones of borrow pits;
- they support floods or spilling not only in service but also during
construction.
Most
RCC dams are gravity dams, although in some countries (South Africa,
China) there are some examples of arch - gravity dams.
For
many years [3-25], the so-called "rolled concrete" was used
as sub-base of roads and airfield pavements where it has generally been
referred to as "lean concrete" or "dry lean concrete".
Mainly, it has been used as a 150 to 250-mm thick base under bituminous
surfacing.
The popularity of rolled concrete for this use has been attributed to
a number of factors, primarily that it is a simple material to produce
and place, and it requires no unique construction facilities or equipment.
The mixtures for paving work usually have low cement content, about
110 to 120kg/m3, and involve the use of washed aggregates suitable for
plain concrete. The water content is chosen to produce no-slump concrete
to suit compaction by rolling, and the material is laid without contraction
joints. The main deficiency, from a performance point of view, has been
the occurrence of transverse cracks. This undesirable characteristic
has had a major influence on mixture proportioning and pavement design.
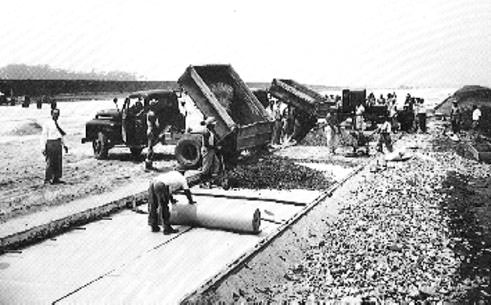
Figure 3.05- Paving works
at Congonhas Airport (São Paulo, Brazil 1950). No-slump concrete
[3-28].
During the construction
of the Congonhas Airport in São Paulo, Brazil [3-28] a dry mixture
was compacted with vibratory plate for paving work.
As
mentioned before, the Alpe Gera Dam is an important milestone in the
development of new construction methods for concrete dams.
The possible merits of dry lean concrete as an interior concrete for
gravity dams were suggested by Paton [3-29; 3-30] in a contribution
to the International Commission on Large Dams (ICOLD).
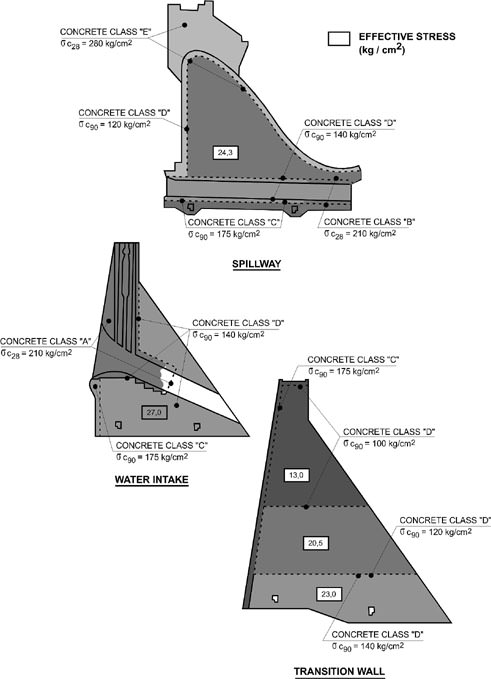
Note: It is important
to point the concept of an upstream concrete membrane used as impermeable
barrier and a massive zone at dowsntream
Figure
3.06-Concrete Class zoning for some Brazilian Dams[3-34].
Although
mass sections using large aggregate RCC were not new, Raphael's paper
[3-31] was the first to recognise that these construction methods could
be used to produce a large dam. Sly Creek Dam for the Oroville-Wyandotte
Irrigation District was designed as an 18-m high solid soil-cement dam
in 1967. The California Division of Safety of Dams approved the design
by a private consulting firm for construction, but it was not built
due to a funding problem [3-32]. RCC (called "rollcrete" at
the time) containing coarse pit-run aggregate was used for the mass
foundation to support the outlet conduit for Cochiti Dam in New Mexico
in 1968 [3-33].
During
the 70's, similar ideas for interior lean mass concrete were adopted
by Brazilian dam designers and government agencies, for massive structures
using CVC as schematic shown on Figures 3.04 [3-34]
Cannon
(1972, 1974), from the Tennessee Valley Authority (TVA), presented papers
entitled "Concrete Dam Construction Using Earth Compaction Methods"[3.35]
and "Compaction of Mass Concrete with Vibratory Roller"[3.36]
in which he showed results from tests conducted by the TVA on concrete
compacted by vibratory roller. These results were obtained in part from
the first full-scale trial of roller compacted concrete in the USA which
took place at Tims Ford Dam in 1970.
In Japan, the Ministry of Construction of the Japanese Government organized
a committee formed by specialists in concrete dams headed by Dr. Kokubu,
and since 1974, this committee has been promoting research concerning
construction of concrete dams. Part of this research is the work being
done on the Roller Compacted Dam (RCD) construction method which has
been investigated independently in Japan [3-11; 3-12; 3-19; 3-37 and
3-38]. A full-scale test conducted at the cofferdam of Ohkawa Dam (volume
= 10,000m3)[3-11 and 3-39] in 1976, and the results of basic research
and studies proved the RCD method applicable to the dam body.
Shimajigawa
Dam [3-37; 3-40], the world's first RCD dam (volume = 317,000m3) was
completed in 1980, followed by Tamagawa Dam [3-40; 3-41; 3-42; 3-43],
the world's largest and highest RCD dam (height=100m, volume 1,150,
000 m3, completed in 1987).
In the UK, Price (1977) conducted a comprehensive laboratory investigation
and design study at the University of Newcastle [3-44]. Trials with
lean concrete which contained fly-ash pozzolana were carried out in
1976 at the Tamar Treatment Works in Cornwall, and the results were
reported by Dunstan (1977) of the South West Water Authority [3-45].
Subsequently, Dunstan played a major role in the CIRIA - Construction
Industry Research and Information Association- sponsored research project
in 1978-80, which included two large and three small full-scale trials
reported in two notes [3-46; 3-47]. In these trials, rolled concrete
with a low cement content and a high fly-ash content was investigated.
A method of using an offset slipform paver to form the face of a dam
was also investigated. The experiments culminated in construction of
a small section of dam using materials and a production plant, which
would be available for the future construction of the Milton Brook Dam,
UK.
The remedial work on Tarbela Dam, Pakistan [3-04 to 3-10], during 1975-83,
was also significant in the historical development of roller compacted
concrete.
One of the first effective uses of RCC in the United States was in 1976
at TVA's Bellefonte Nuclear Plant [3-48], where 5,800 m3 were used to
raise the supporting base under the turbine building by approximately
10 ft. Between 1978 and 1980, the USCE used RCC on the floodway sill
adjacent to the Tanana River, [3-49] on the Chena River project in Alaska,
[3-50] and for rock protection in the tailrace of the second powerhouse
at Bonneville Lock and Dam in Washington.
Based
on data developed in its early research and test sections, the Corps
designed an alternate RCC for Zintel Canyon Dam near Kennewick, Washington,
in 1974. The concept of a more economical gravity dam took a big step
forward when it was found that the "rockfill" section could
be reduced to a typical gravity dam section with a vertical upstream
face [3-13; 3-51]. Although Zintel Canyon Dam was not built due to lack
of funds, many of its concepts were carried through at Willow Creek
Dam, Oregon, This dam, completed in 1982, became the world's first major
dam built almost entirely of RCC. A large amount of RCC was used for
roads and runways at Ft. Drum Army Base in New York State in 1980.
The
53-m high Willow Creek Dam confirmed the economy and rapid construction
possible with RCC. More than 315,000 m3 of RCC were placed in less than
5 months at an approximate cost of US $30/m3, including the precast
concrete panels that formed the vertical upstream face and all incidental
costs for the RCC mass [3-52].
The
experiments at Tamar Treatment Works (Cornwall, 1976), reported by Dunstan,
included two large and three small full-scale tests with low cement
and high fly-ash content using an offset slipform paver to form the
face of a dam. These did not lead to the use of RCC in a major dam in
the UK, but were the basis for the U.S. Bureau of Reclamation's (USBR)
design for Upper Stillwater Dam, Utah. [3-53]. The 92-m high Upper Stillwater
Dam, completed in 1987, contains 1,080,000 m3 of RCC placed within horizontally
slipformed, air-entrained concrete facing elements.
Canada was also an early user of RCC technology: the cofferdam for Revelstoke
Dam in British Columbia was completed in 1980 [3-54].
The Japanese and Canadian projects are also worthy of note for using
forced mixing rather than conventional concrete batch drum mixing.
Since these first projects, RCC has rapidly gained popularity and has
been used in a number of completed structures in Brazil [3-55], Spain,
France, Australia, and South Africa as well as in the United States
and Japan. RCC is being used in other structures that are in various
stages of concept, design, and construction. As with conventional concrete,
there does not appear to be a limit to the size of the structure that
can be designed and built with RCC.
RCC
is also used as dam facing for erosion protection on new and existing
embankment dams.
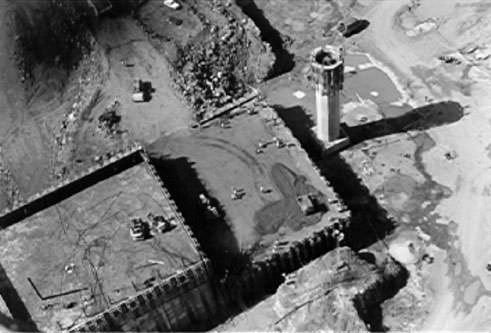
Figure 3.07-RCC placed
at the Navigation lock of Tucurui Dam - Brazil
|